Boiinnggggg! Spring has sprung! Ok, maybe not in meteorological terms, but certainly in restoration terms because today found me back in the garage.
You may recall that last time I had offered up the yellow "new" rear lamp panel to the car's now rather bare rear end. It fitted ok, but it still needed a lot of prep on the areas where it would be welded, plus I wanted to make sure the boot would fit well. To adapt an old phrase "it's a long time welded", so it is important to get this right.
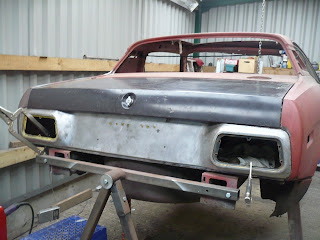 |
Nice ar*e. |
The new boot was bolted in place after having one of those nice moments when you remember you have a handy part in the shed. Some time ago I bought a new set of bolts & washers for this job, so once e again things are coming out of the shed and going on the car.
The boot fitted ok, but was low at the nearside. After much head scratching my friend Neil pointed out that the nearside hinge itself had an awful lot of play in it, so we took the boot off again to investigate. It soon became clear that the spot welds which hold the plate, to which the hinges bolt, had broken. A bit of MIG later and all was well. The boot was then reattached and to my joy I discovered that not only is there adjustment in the boot-to-hinge bolts, but also in the hinge-to-body. So with quite a lot of fiddling, the boot was made to sit at the right height and latitude. Sort of.
Fed up with having to use a block of wood to prop the boot lid open, and in fear of it crashing down on my head, the next job was to fit the boot stay bracket. This was drilled off the old section of wing and after being cleaned up, was plug welded in place.
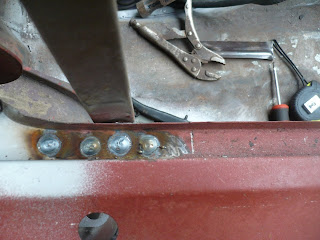 |
Boot stay bracket plug welded in place. |
Quite a bit of time was spent cleaning up the edges of the new panel and the wings/boot floor ready for welding. I am terrible for letting my heart rule my head, but today I resisted the urge to just weld it all up and worry about any errors afterwards. This needs to be spot-on so it will only be welded when I am happy with the fit of everything. So that just leaves the boot floor, then. Hmmmmm.
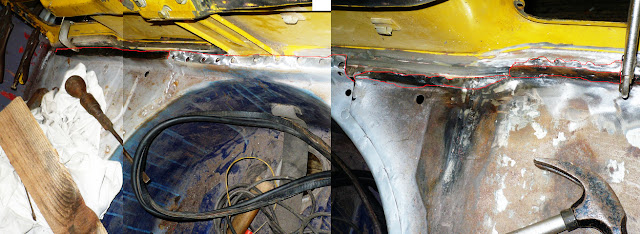 |
Made of 3 photos, this shows (with the help of the red lines) what is left of the boot floor lip. |
In one of my previous posts I mentioned that the lip of the boot floor to the bottom edge of the lamp panel is all over the place. At some points it lips over the panel, at others it is miles to high and in other areas it doesn't meet it at all. I know that Speke build quality was bad (see boot hinges, above), but surely it cannot have been designed this way. I can only assume that someone has repaired it badly before, by cutting off random bits of boot floor and welding whatever was left to whatever was available.
Sadly the only decent solution I can think of is to cut off all of the boot floor lip, leaving just the flat of the boot floor, and fabricate a new one to fit the panel. Incidentally, it was like this with the old panel in place, too.
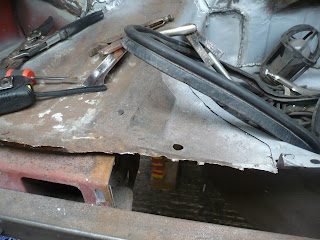 |
Nearside boot floor. Lip or no lip? |
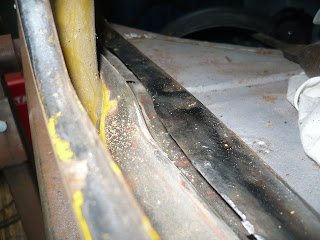 |
Can you guess which part of the car this is? |
I'll keep you posted on what happens next.